
Teacher's Report
Bill Hanshumaker, Educator at Sea
Researcher Interview:
Jon Bumgardner
Mechanical engineer
NOAA Pacific Marine Environmental Laboratory
B.S. in Mechanical Engineering (2001), University of Washington
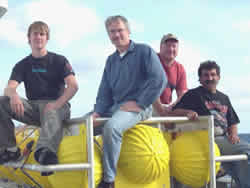
PMEL engineers
and UW chemist atop the RAS. Left to right: Jon Bumgardner - PMEL
(see interview), Dave Butterfield - UW/PMEL chemist, Nick Delich -
PMEL, John Shanley - PMEL. |
|
Bill:
When you started in college, was this what you thought you would do?
Jon:
Absolutely not! I thought that I would end up in a design firm or big
factory in the automotive industry or aerospace. But I had a real interest
in designing oceanographic equipment.
Bill:
So, how did you get into it?
Jon:
Actually, I was in the right place at the right time. I received an email
about the job opening while at UW, and my present supervisor was also
from UW. After a successful interview, I got the job.
Bill:
Describe what you do.
Jon:
What I mainly do is mechanical design. The scientists approach us with
either the needs of their instrument, or they need a certain type of data
and we design the instrument. Electrical engineers design the circuit
board and control software. Mechanical engineers design pressure casings,
seals, ballasting and other structural needs. We also work on the geometric
design of the instrument platform and try to integrate all the different
design needs. With 3-D modeling software we can test and evaluate these
designs on a computer. For example, the Remote Access Sampler (RAS) frame
was modeled using factors such as its weight, center of gravity and how
it will sit on the ocean bottom. We can use the computer software to test
its structural strength by applying different weight at the ends or trying
to bend it. We can separate the frame into components and do structural
analysis. Then we pull it back together and do mechanical drawings. Those
are sent to the shop for fabrication. Using the drawings, I work with
fabricators, welders and machinists until we come up with the final instrument.
|
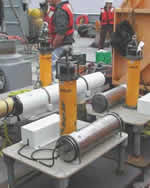
Two bottom pressure recorders (BPR) were deployed
this evening at Axial. BPRs are in the two instruments front and right.
In the background is the ocean bottom hydrophone (OBH) deployed at
the start of the expedition. |
Bill:
What's your current project here on the Thompson?
Jon:
I'm currently working on NeMO Net, which is a joint NOAA, University of
Washington and Oregon State University project. I designed the RAS,
and I'm here to be sure that it is deployed properly. It has 50 bottles
to take water samples while actively measuring temperature and pH. It
also has an acoustic release so that it can be remotely recovered.
After sending an acoustic signal from the Thompson, the RAS drops its
anchor and floats to the surface for recovery. We integrate
communications with an acoustic modem and a self-leveling mount so that
it points up. This enables communication to the buoy and then back to
the lab.
Bill:
How much of the information is communicated in real time and what
information is stored and must be retrieved later?
Jon:
Bottom pressure and temperature are communicated in near
real-time daily at the NeMO Net web site (http://www.pmel.noaa.gov/eoi/nemo/realtime).
The fluid from the hydrothermal vents is sucked up from three locations
for comparison.
Bill:
What's the most difficult problem that you encountered?
Jon:
Because it does so many things, this particular package is a monster.
It's very heavy; weighing about as much as a small sports car. It's
hard to move around deck, and moving it can be very dangerous if the
ship's deck is also moving. Obviously we have an excellent crew on the
Thompson, but it is an issue moving something this big while at sea. A
critical design challenge was to make it small enough for deployment.
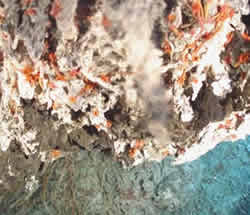
Sulfide
worms (bright orange near top of image) near the top of Hell sulfide
structure. A photo/video survey was performed to observe feeding behavior
and the territoriality of the worms. |
|
Bill:
Looking into the future, how do you see yourself involved?
Jon:
I see a more complex, multi-noded NeMO Net. There are two
sides to the
challenge. There's the scientific side, crafting the questions that
need answering. Then there's the technological side, designing
instruments to answer those questions. Perhaps the future will bring
remote controlled devices like the lunar crawler, which can be directed
from land to carry out deep-sea sampling. There will be less dependence
on ship-dependent devices like ROPOS. The future will be quicker and
more mobile, more like a living real time observatory.
|